Impact Crushers |
<500mm |
10:1 to
“`html
Construction Waste Crushing Plant: Efficient Recycling for Sustainable Construction
Construction Waste Crushing Plant: Turning Debris Into Valuable Resources
The modern construction industry generates massive amounts of waste, but a construction waste crushing plant offers an eco-friendly solution. These specialized facilities process demolition debris into reusable aggregates, helping reduce landfill dependency while supporting circular economy principles.
Key Components of a Construction Waste Crushing Plant
An effective construction waste crushing plant typically includes:
- Primary jaw crushers for initial size reduction
- Secondary impact crushers for finer processing
- Trommel screens for material separation
- Magnetic separators for metal recovery
- Conveyor systems for efficient material handling
How Construction Waste Crushing Plants Process Materials
The operation of a construction waste crushing plant follows these stages:
- Sorting: Manual or mechanical separation of different waste types
- Pre-screening: Removal of oversized or contaminated materials
- Crushing: Multi-stage reduction of concrete, bricks, and asphalt
- Screening: Grading materials into different size fractions
- Final sorting: Additional quality control before stockpiling
The Environmental Benefits of Construction Waste Crushing Plants
A well-designed construction waste crushing plant delivers significant ecological advantages:
- Cuts landfill use by 70-90%: Diverts demolition waste from disposal sites
- Saves natural resources: Recycled aggregates replace virgin materials in new
An Artificial Sand Making Plant (also known as a Manufactured Sand (M-Sand) Plant) is a facility designed to produce high-quality sand from rocks, gravel, or industrial byproducts like slag. It serves as an eco-friendly alternative to natural river sand, which is depleting due to over-mining and environmental concerns.
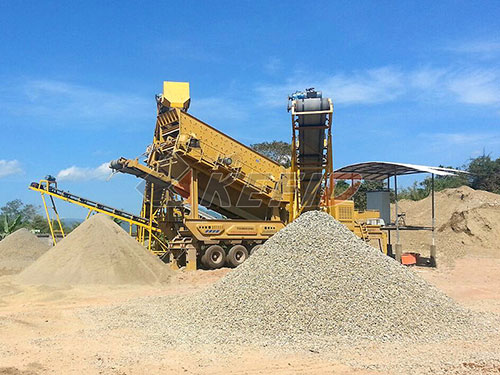
Key Components of an Artificial Sand Making Plant
1. Primary Crusher
– Jaw crusher or gyratory crusher breaks large rocks into smaller pieces (~40-50mm).
2. Secondary Crusher
– Cone crusher or impact crusher further crushes material into finer sizes (~20-30mm).
3. Sand Making Machine (Vertical Shaft Impactor – VSI)
– The core equipment that shapes crushed stone into cubical sand particles by high-speed impact crushing.
4. Vibrating Screen
– Separates sand into different sizes (e.g., coarse, medium, fine).
5. Sand Washer (Optional)
– Removes dust and impurities to improve quality (for high-grade construction use).
6. Conveyor System
– Transports raw materials and finished products between machines.
7. Dust Control System
– Reduces airborne particles using water spray or bag filters for environmental compliance.
Types of Raw Materials Used
– Hard rocks (granite, basalt)
– Limestone
– River pebbles
– Industrial waste (slag, recycled concrete)
Advantages of Artificial Sand
✔ Consistent Quality – Controlled particle shape & gradation.
✔ Eco-Friendly – Reduces riverbed mining and environmental damage.
✔ Cost-Effective – Lower transportation costs if sourced locally.
✔ Better Workability – Cubical-shaped grains enhance concrete strength.
Applications
– Concrete production
– Road construction
– Plastering & masonry work
– Precast elements & RCC structures
Challenges & Solutions
1. High Dust Generation → Install dust suppression systems.
2. Uneven Gradation → Optimize crushing & scr
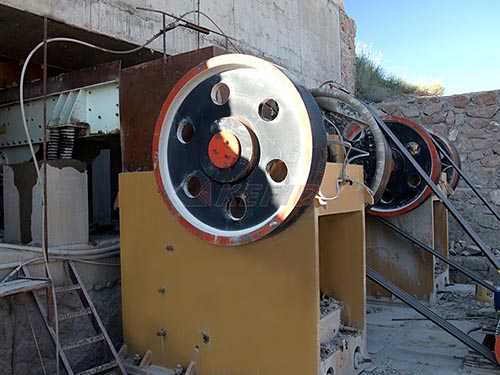
ing processes.
3. Moisture Control → Use dry processing or sand drying systems if needed.
Plant Setup Considerations
✅ Raw material availability & hardness
✅ Required production capacity (e.g., 50 TPH, 200 TPH
An Aggregate Crushing Plant is a facility designed to process raw materials like rocks, sand, and gravel into various sizes of aggregate used in construction, road building, and other infrastructure projects. Here’s a breakdown of its key components and processes:
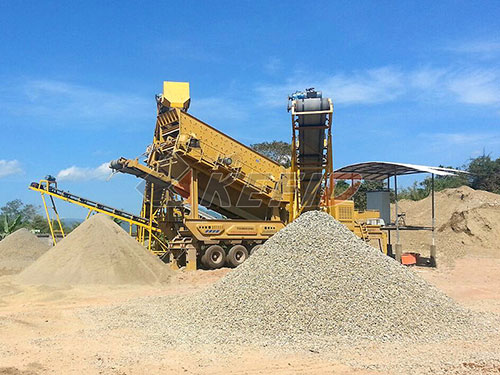
1. Components of an Aggregate Crushing Plant
– Primary Crusher:
– Breaks down large rocks (e.g., jaw crusher, gyratory crusher).
– Output: Coarse aggregates (e.g., 150–50 mm).
– Secondary Crusher:
– Further reduces material size (e.g., cone crusher, impact crusher).
– Output: Medium aggregates (e.g., 50–20 mm).
– Tertiary/Quaternary Crushers:
– Produces fine aggregates or sand (e.g., VSI crusher).
– Output: 20–5 mm or smaller.
– Screening Equipment:
– Vibrating screens separate crushed material into different sizes.
– Conveyor Belts:
– Transport material between stages.
– Washing Systems (optional):
– Remove dirt/clay (for high-quality sand/gravel).
– Storage Bins/Silos:
– Hold finished products before shipment.
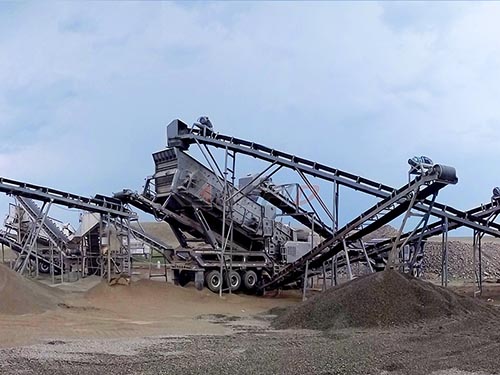
2. Types of Aggregates Produced
– Coarse Aggregates (>4.75 mm): Used in concrete mixes, road bases.
– Fine Aggregates (<4.75 mm): Sand for mortar, asphalt.
– Specialty Aggregates: Railway ballast, drainage stones.
3. Process Flow
1. Feeding: Raw material dumped into a hopper.
2. Crushing: Multi-stage reduction (primary → secondary → tertiary).
3. Screening: Sized via vibrating screens; oversize recirculated.
4. Washing (if needed): Removes impurities.
5. Stockpiling: Sorted aggregates stored for dispatch.
4. Key Considerations
– Material Hardness: Dictates crusher type (e.g., jaw for granite, impact for limestone).
– Capacity: Ranges from small portable plants (100 TPH) to large setups (1000+ TPH).
– Environmental Controls: Dust suppression, noise barriers, water recycling.
A crushing plant is a facility that processes raw materials (such as rocks, ores, or recycled concrete) into smaller, usable aggregates. The capacity of a crushing plant refers to the maximum amount of material it can process per hour (or per day). Different capacity crushing plants are designed to meet various production needs, from small-scale operations to large industrial projects.
Types of Crushing Plants by Capacity
Crushing plants can be categorized based on their production capacity:
1. Small Capacity Crushing Plant (10–50 TPH)
– Suitable for small quarries, construction sites, or recycling operations.
– Common equipment:
– Small jaw crusher
– Impact crusher or cone crusher
– Vibrating screen
– Small belt conveyors
2. Medium Capacity Crushing Plant (50–300 TPH)
– Used in medium-sized mining or construction projects.
– Common equipment:
– Primary jaw crusher + secondary cone/impact crusher
– Multiple vibrating screens for better grading
– Feeders and conveyors
3. Large Capacity Crushing Plant (300–1000+ TPH)
– Designed for large-scale mining, highway construction, or cement production.
– Common equipment:
– Large primary gyratory/jaw crusher + multiple secondary/tertiary crushers
– High-capacity screens and conveyors
– Automated control systems
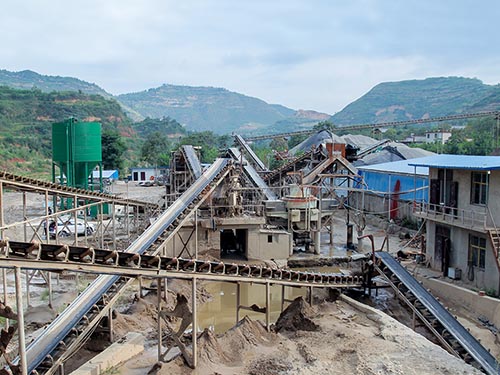
Factors Affecting Crushing Plant Capacity
– Material hardness & abrasiveness (softer materials allow higher throughput).
– Feed size & required output size (finer products reduce capacity).
– Crusher type & configuration (jaw, cone, impact, vsi).
– Screening efficiency (proper screening ensures smooth operation).
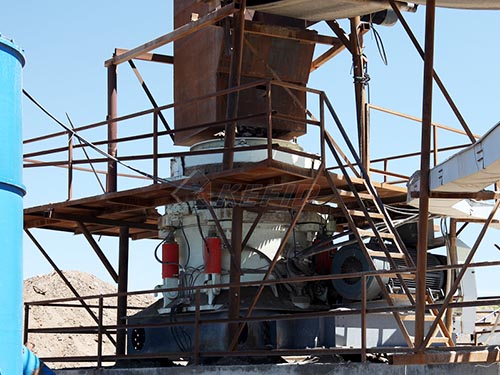
Choosing the Right Capacity
– For small contractors → 50–100 TPH plants.
– For aggregate producers → 200–500 TPH plants.
– For mining/quarrying → 500–1000+ TPH plants.
Would you like recommendations for a specific application?
A Hard Stone Crushing Plant is designed to process tough, abrasive materials like granite, basalt, quartz, and other high-hardness rocks. These plants are widely used in mining, construction, and aggregate industries to produce high-quality crushed stone for roads, concrete, and other applications.
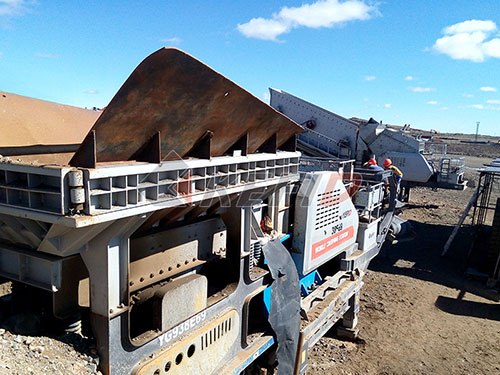
Key Components of a Hard Stone Crushing Plant
1. Primary Crusher
– Jaw Crusher: Ideal for initial crushing of large, hard stones (e.g., granite, basalt).
– Gyratory Crusher: Suitable for very large feed sizes in mining operations.
2. Secondary Crusher
– Cone Crusher: Best for medium-to-hard stones (e.g., river pebbles, quartz).
– Impact Crusher: Used for softer but still hard materials (e.g., limestone with high abrasiveness).
3. Tertiary/Quaternary Crushers (Fine Crushing & Shaping)
– Vertical Shaft Impact (VSI) Crusher: Produces well-shaped sand and fine aggregates.
– High-Pressure Grinding Roll (HPGR): Used for ultra-fine crushing in some advanced plants.
4. Screening Equipment
– Vibrating screens separate crushed material into different sizes (e.g., 0-5mm, 5-20mm, 20-40mm).
5. Conveyors & Feeders
– Belt conveyors transport material between stages.
– Vibrating feeders ensure steady material flow.
6. Dust Suppression System
– Water spray or mist systems reduce dust emissions.
7. Control System
– PLC-based automation ensures efficient operation.
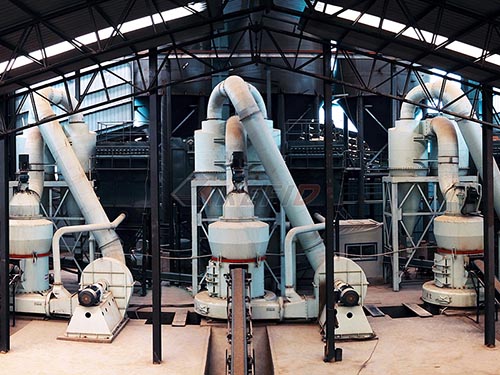
Typical Hard Stone Crushing Process
1. Blasting & Loading (if from a quarry) → Primary crushing → Secondary crushing → Screening → Tertiary shaping → Final screening → Stockpiling.
2. If producing sand: Additional VSI crushers + sand washing machines may be included.
Considerations for Hard Stone Crushing
– Wear Resistance: Use high-manganese steel or ceramic liners in crushers to handle abrasiveness.
– Energy Efficiency: Cone crushers are more efficient than jaw crushers for secondary crushing.
– Moisture Content: Wet processing may be needed if the stone contains clay or dirt.
– Final Product Requirements: Adjust crusher settings based on desired output
A soft stone crushing plant is designed to process relatively easy-to-crush materials such as limestone, marble, gypsum, dolomite, or chalk. These stones have lower hardness (typically Mohs 3-5) compared to hard rocks like granite or basalt. Below is a detailed breakdown of a soft stone crushing plant setup:
1. Key Components of a Soft Stone Crushing Plant
# (1) Primary Crushing Stage
– Jaw Crusher (Recommended for coarse crushing)
– Handles large feed size (up to 1,200 mm).
– Produces output of ~150-300 mm.
– Impact Crusher (Alternative for softer stones)
– Better for less abrasive materials.
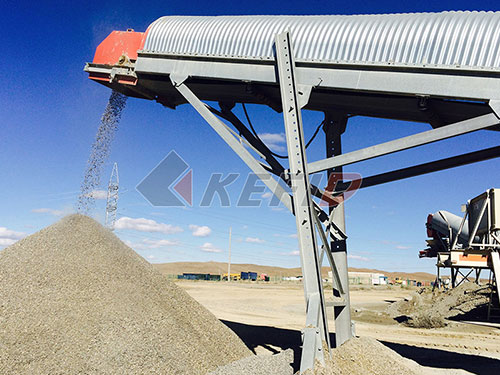
# (2) Secondary Crushing Stage
– Cone Crusher (For medium-hardness stones)
– Produces well-shaped aggregates (~20-70 mm).
– Impact Crusher (Preferred for softer stones like limestone)
– Provides better cubical shape.
# (3) Tertiary/Fine Crushing Stage (Optional)
– Vertical Shaft Impact (VSI) Crusher or Hammer Crusher
– Produces sand or fine aggregates (~0-5 mm).
# (4) Screening & Grading
– Vibrating Screen separates different sizes (e.g., 0-5mm, 5-10mm, 10-20mm).
# (5) Conveyor System & Dust Control
– Belt conveyors transport materials between stages.
– Dust suppression systems reduce airborne particles.
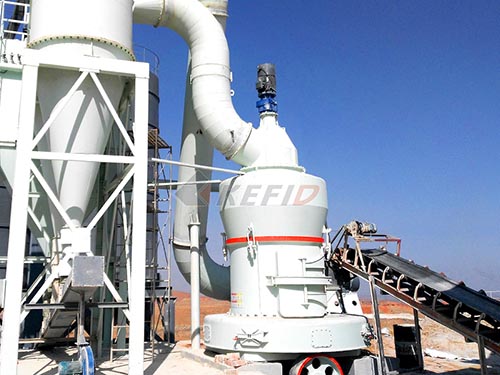
2. Typical Flow Process
1. Feeding: Raw material is loaded into a hopper via an excavator or wheel loader.
2. Primary Crushing: Jaw crusher reduces large chunks to ~150-300 mm.
3. Secondary Crushing: Cone/impact crusher further breaks down to ~20-70 mm.
4. Screening: Separates aggregates into required sizes; oversize goes back for recrushing.
5. (Optional) Sand Making: VSI crusher produces fine sand if needed.
3. Recommended Equipment Selection
| Material | Primary Crusher | Secondary Crusher | Fine Crusher |
|-|-||-|
| Limestone | Jaw Crus
The SP Series Vibrating Feeder is a type of industrial equipment designed to efficiently and uniformly feed bulk materials to crushers, conveyors, or other processing machinery. It is widely used in mining, metallurgy, construction, and other industries for handling granular or lumpy materials.
Key Features of SP Series Vibrating Feeder:
1. Stable & Reliable Operation
– Uses a vibrating motor or electromagnetic exciter to generate vibrations, ensuring smooth material flow.
– Minimal maintenance due to simple structure and durable components.
2. Adjustable Feeding Rate
– The feeding speed can be controlled by adjusting the vibration amplitude or frequency.
– Suitable for different material types (fine powders to large lumps).
3. Durable Construction
– Made of high-quality steel with wear-resistant liners (if required).
– Resistant to impact and abrasion.
4. Energy Efficient
– Low power consumption compared to belt feeders or screw feeders.
– Designed for continuous operation with minimal energy loss.
5. Wide Application Range
– Used in mining (ore feeding), aggregate production, cement plants, recycling, and chemical industries.
– Can handle materials like coal, ore, gravel, sand, chemicals, and more.
Technical Specifications (General)
– Capacity: Ranges from a few tons per hour up to hundreds of tons per hour (depending on model).
– Max. Feed Size: Up to 500mm (varies by model).
– Power Source: Electric motor (vibratory mechanism).
– Installation: Can be mounted horizontally or at a slight incline.
Advantages Over Other Feeders
✔ Better control over material flow compared to belt feeders.
✔ Less clogging than screw feeders when handling sticky materials.
✔ Lower maintenance than apron feeders for heavy-duty applications.
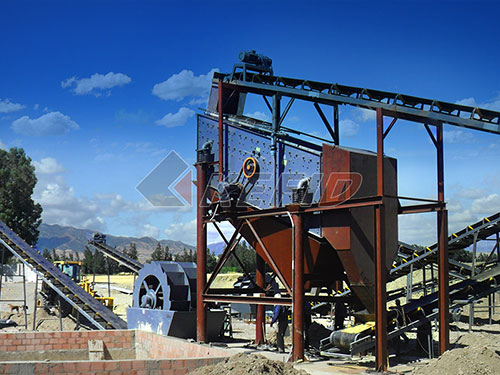
Common Applications
– Feeding jaw crushers or impact crushers in crushing plants.
– Pre-screening material
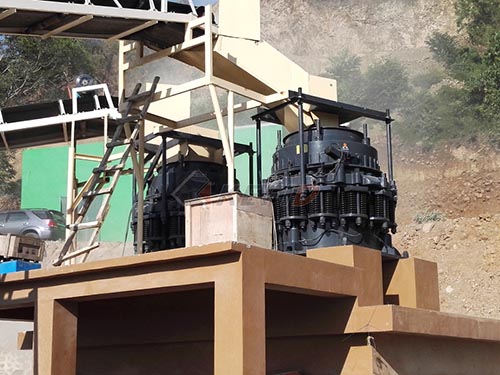
efore processing.
– Uniform feeding in conveyor systems.
– Batch feeding in mixing or batching plants.
Manufacturers & Variations
Different manufacturers may offer variations in design (electromagnetic vs. motor-driven), size, and features. Well-known brands include:
– Metso (Nordberg)
– Sandvik
– Terex
– Syntron (FMC Technologies)
– Chinese manufacturers like Liming Heavy Industry, etc.
Would you like details
|